Metalurgia e Fundição
Produção de Aço Líquido
Atualmente são utilizadas quatro vias para a produção de aço: a via clássica de alto-forno/forno básico a oxigénio, a fusão direta de sucata (Forno de Arco Elétrico - FAE), a redução por fundição e a redução direta:
- Na via de alto-forno/forno básico a oxigénio, a gusa é produzida utilizando maioritariamente minério de ferro (70 – 100 %) e coque num alto-forno e depois transformado em aço num forno básico a oxigénio. A inclusão de operações de fabrico e sinterização de coque, faz com que esta via seja altamente intensiva em energia;
- Na fusão direta de sucata num FAE, a sucata é usada como fonte de ferro e a intensidade energética é significativamente inferior à da via de alto-forno/forno básico a oxigénio, uma vez que não são necessários os processos de fabrico de ferro e coque;
- A redução por fundição está associada à produção de metal quente a partir de minério de ferro sem coque. Esta via apresenta duas unidades: na primeira, o minério de ferro é aquecido e reduzido por gases gerados na segunda unidade, um fundidor-gasificador alimentado com carvão e oxigénio. O minério parcialmente reduzido é então fundido na segunda unidade, produzindo o metal quente líquido ou (em alguns casos) aço líquido;
- A redução direta envolve a produção de ferro primário sólido a partir de minérios de ferro (e frequentemente também sucata) e um agente redutor (por exemplo, gás natural). O produto sólido é chamado ferro diretamente reduzido e é principalmente aplicado como matéria-prima em fornos de arco elétrico.
Em 2019, a produção de aço bruto na UE-28 baseou-se na via de alto-forno/forno básico a oxigénio (58,6 %) e na via do FAE (41,4 %). Na UE-28 não existem unidades de redução por fundição em escala comercial.
Em Portugal existem apenas dois fornos de arco elétrico nas unidades de produção da Siderurgia Nacional S.A. (detida pelo grupo Megasa) na Maia com uma capacidade de produção anual de 600 kt e no Seixal com uma capacidade anual de 1 100 kt. 1 Estas unidades são especializadas no fabrico de fio-máquina de baixo, médio e alto carbono e varões de aço nervurado (barras) para armadura de betão, em diferentes apresentações; barra, bobine, spool e carrete. 2
Uma vez que em Portugal só se produz aço a partir da fusão direta de sucata em FAE, apenas esta tecnologia será descrita em seguida.
Preparação da Sucata
A sucata é normalmente carregada em cestos através de ímanes ou garras. O principal requisito para a utilização de sucata é um requisito de inclusão mínima não metálica, em especial de materiais não magnéticos e metais não ferrosos. Para garantir que não são incluídos contaminantes perigosos ou material radioativo, antes do carregamento é necessário efetuar alguma triagem da sucata. A sucata pode ser também pré-aquecida (utilizando frequentemente o calor residual do processo) para reduzir a necessidade de energia na fusão no interior do forno.
Preparação do ferro diretamente reduzido
Neste processo, o ferro é diretamente reduzido no seu estado sólido, podendo existir diferentes tipos de reatores:
- Forno de eixo;
- Forno rotativo;
- Forno de forja rotativa (não existem em Portugal);
- Reator de leito fluidizado.
Na redução direta do ferro, não se passa pela fase de fusão nem pela fase de escória para se efetuar a redução. Os contaminantes que normalmente são removidos durante a fusão e a escória permanecem dentro do ferro diretamente reduzido e são separados no FAE, levando a um maior consumo de energia do que a alternativa da fusão de sucata.
Uma forma de reduzir o consumo de energia no FAE, pode ser enviar diretamente o ferro fundido do reator para o FAE, aproveitando pelo menos o calor ainda presente no material após a redução.
Forno de arco elétrico
Num FAE, a sucata e/ou as unidades de ferro fabricadas (tais como ferro diretamente reduzido, gusa, ou carboneto de ferro) são fundidos e convertidos em aço de alta qualidade, utilizando arcos elétricos de alta potência formados entre um cátodo e um (no caso de corrente contínua) ou três (no caso de corrente alternada) ânodos. A sucata é de longe o recurso mais importante, representando cerca de 80 % de toda a matéria-prima metálica do FAE. Esta tecnologia permite evitar o processo de pirólise do carvão e o processo de redução do minério de ferro, energeticamente mais intensivos.
As unidades de ferro são carregadas num cesto juntamente com pedra calcária (para a formação de escória) e alimentadas ao forno. A principal tarefa da maioria dos fornos de arco elétrico modernos é converter as matérias‑primas sólidas em aço bruto líquido o mais rapidamente possível, implementando uma refinação adicional em processos posteriores de produção secundária de aço. Após a fusão e antes das operações siderúrgicas secundárias, é mantido um período de operação de banho plano. A injeção de oxigénio e a injeção de carvão em pó são operações comuns de tratamento.
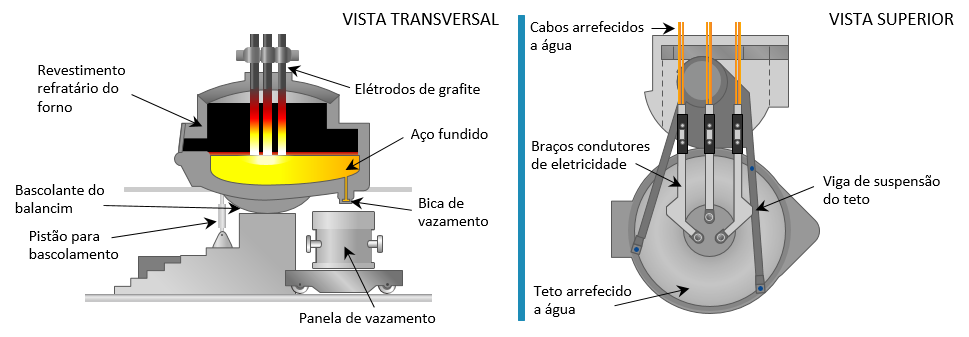
Esquema de um forno de arco elétrico. Adaptado de 3
Medidas e Tecnologias na Produção de Aço em FAE a partir de sucata
Tecnologia ou Medida |
Impacto na Eficiência Energética |
Estado de Desenvolvimento |
---|---|---|
Redução de 10 - 15 % do consumo de energia |
Comercial |
|
Sem Informação |
Comercial |
|
Redução de 11 - 22 kWh/t de aço |
Comercial |
|
Redução de 0,068 GJ/t de aço |
Comercial |
|
Redução de 6 - 8 kWh/t de aço |
Comercial |
|
Redução de 0,14 GJ/t de aço |
Comercial |
|
Redução de 100 kWh/t de aço |
Comercial |
|
Redução de 6 - 11 % do consumo de energia |
Comercial |
|
Redução de 220 kWh/t de aço |
Tecnologia Emergente |
|
Redução de 3 % do consumo de energia |
Tecnologia Emergente |